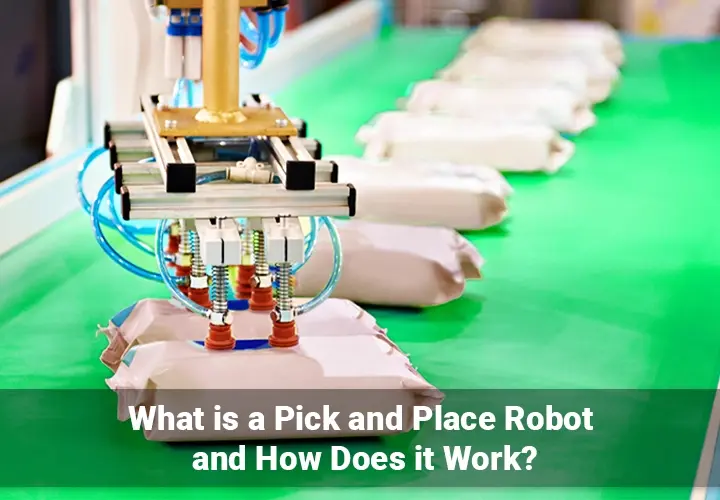
Introduction
In today’s fast-paced manufacturing world, efficiency and precision are critical. Industries like food processing, electronics, automotive, and pharmaceuticals rely heavily on automation to meet increasing production demands. Among the most essential automation solutions are Pick and Place Robots. These intelligent machines handle repetitive, labour-intensive tasks quickly and accurately, freeing human workers for more strategic and complex roles.
In this guide, we’ll dive deep into what pick and place robots are, how they work, their history, types, applications, advantages, and how to choose the right one for your business.
What is a Pick and Place Robot?
A pick and place robot is an automated machine used in industrial settings to quickly and accurately lift items from one location and place them in another. Commonly deployed in sectors like manufacturing, packaging, logistics, food processing, and electronics, these robots streamline repetitive tasks such as sorting, assembling, and palletizing. With advanced sensors and programmable arms, pick and place robots enhance production speed, reduce human error, and improve overall efficiency in high-volume operations.
History of Pick and Place Robots
The history of pick and place robots traces back to the dawn of industrial automation, evolving from early mechanical systems to today’s high-speed, intelligent machines. These robots have become essential in manufacturing, logistics, electronics, and food processing, transforming repetitive tasks into efficient, automated operations.
Early Innovations (1960s)
The journey began with Unimate, the first industrial robot, invented by George Devol and Joseph Engelberger in the early 1960s. Unimate was designed to handle heavy die-cast parts and weld them onto car bodies. This breakthrough marked the birth of robotic automation in manufacturing and laid the foundation for specialised robotic arms.
Rise of the SCARA Arm (Late 1970s)
In the late 1970s, Hiroshi Makino introduced the SCARA (Selective Compliance Assembly Robot Arm). Unlike traditional robots, SCARA arms offered speed, rigidity, and selective compliance in the horizontal plane—perfect for tasks like inserting electronic components or assembling small parts. This innovation dramatically improved throughput in precision assembly environments.
The Delta Robot Revolution (1980s–1990s)
A major turning point came in the early 1980s with the development of the Delta robot by Professor Reymond Clavel and his team at the École Polytechnique Fédérale de Lausanne (EPFL), Switzerland. The Delta robot’s parallel kinematic structure offered unmatched speed and precision for lightweight pick and place operations.
The design was soon licensed to the Swiss company Demaurex, which facilitated industrial adoption. In 1999, ABB Flexible Automation launched the FlexPicker, a Delta robot that became a game-changer in high-speed pick and place applications—especially in the food packaging industry.
Technological Milestones (2000s and Beyond)
The 2000s saw rapid innovation:
-
Vision Systems: Integration of advanced cameras and AI-based vision systems enabled robots to detect, identify, and handle objects with greater precision.
-
Modular and Multi-Headed Designs: To enhance flexibility and speed, manufacturers introduced modular units and multi-headed robots for simultaneous object handling.
-
Automation and AI: With artificial intelligence, pick and place robots became smarter, capable of learning and optimising tasks, reducing human intervention and increasing output efficiency.
Modern Day Applications
Today’s pick and place robots are highly specialized systems used across sectors like:
-
Electronics (component placement)
-
Pharmaceuticals (precise handling of medical items)
-
Food Processing (packaging, sorting)
-
E-commerce & Logistics (order fulfillment and sorting)
With their speed, precision, and reliability, these robots continue to reshape how products are made, packaged, and shipped.
How Does a Pick and Place Robot Work?
- Object Detection: The robot identifies the object to pick using sensors or vision systems.
- Gripping: The robot employs specialized end effectors (grippers, suction cups, or claws) based on the object’s size, shape, and material.
- Movement: The robotic arm follows a pre-programmed path to lift and transport the object to the designated location.
- Placement: The object is accurately placed by releasing the grip mechanism at the target point.These robots can move objects between stationary surfaces, conveyors, or a combination.
Major Components of a Pick and Place Robot
- Robot Arm (Manipulator): The mechanical structure for reaching and moving.
- End Effector: The “hand” that grips the object.
- Actuators: Motors (servo, stepper, hydraulic) that control movement.
- Sensors: Detect object position, orientation, and sometimes defects.
- Controllers: The “brain” that synchronises movement, vision, and gripping.
Types of Pick and Place Robots
Cartesian Robots
Operate in straight lines along X, Y, and Z axes. Highly precise and simple to program.
SCARA Robots
Fast and flexible, ideal for assembly lines needing lateral movement.
Delta Robots
Lightweight and speedy, it is perfect for high-speed picking (especially food and electronics).
Robotic Arms
5-axis or 6-axis arms capable of intricate movements and orientation adjustments.
Collaborative Robots (Cobots)
Designed to work safely alongside human workers, offering flexibility in smaller workspaces.
Advantages of Pick and Place Robots
- Speed: Execute tasks faster than human workers.
- Precision: Consistent, error-free handling.
- Productivity: Work continuously without fatigue or breaks.
- Safety: Minimise workplace injuries.
- Consistency: Uniform handling across shifts and operations.
- ROI: Lower operating costs compared to manual labour.
- Scalability: Easily adapted to different products and workflows.
Applications of Pick and Place Robots
- Food and Beverage: Packaging, sorting, and placing products on conveyors.
- Electronics: Assembling circuit boards with tiny components.
- Pharmaceuticals: Handling medical devices and packaging medications.
- Automotive: Moving parts, welding, and quality inspections.
- Warehousing: Order picking and sorting.
- Medical: Assisting in surgeries and hospital logistics.
Industries That Use Pick and Place Robots
- Food Processing
- Consumer Electronics
- Automotive Manufacturing
- Medical and Pharmaceutical
- Logistics and Warehousing
- Research Laboratories
How to Choose the Right Pick and Place Robot
When selecting a pick and place robot, consider the following:
- Payload Capacity: What is the weight of the objects?
- Reach and Workspace: How far does the robot need to extend?
- Speed and Cycle Time: How quickly must the robot operate?
- Precision and Repeatability: Is high accuracy critical?
- Integration: Does it fit into your existing systems?
- End Effector Options: Does the application need gripping, suction, or a custom tool?
- Safety Requirements: Especially if working alongside humans.
How Much Do Pick and Place Robots Cost?
- Basic Systems: Starting around $10,000 – $20,000.
- Advanced Systems (with vision systems and complex programming): $40,000 – $50,000+.
While upfront investment may seem high, companies usually recover costs within 1-2 years through increased productivity and reduced labour expenses.
Conclusion
In an era of rapid industrialisation and automation, Pick and Place Robots are no longer optional but essential. By enhancing speed, safety, and operational efficiency, they allow businesses to meet the rising demands of modern consumers while maintaining high standards.
Delta Stark Engineering offers world-class pick and place robotic solutions tailored to your unique needs. Whether you are automating a food packaging line or assembling precision electronics, our expertise ensures the best fit for your production goals.