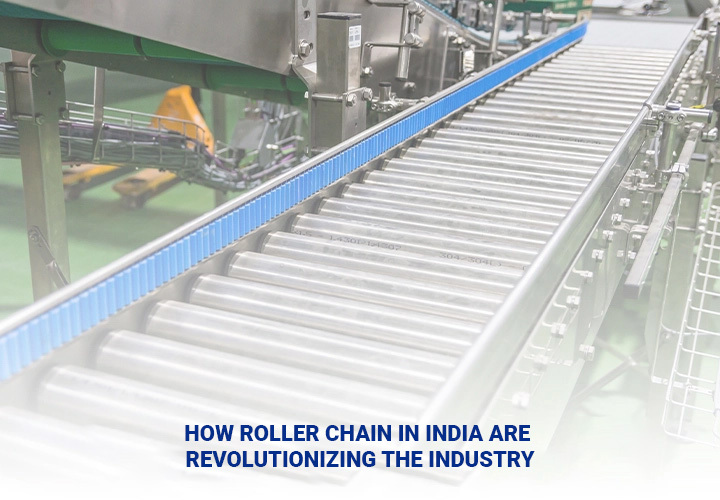
Driven by material advancements and technology, roller chain manufacturers have drastically reshaped their chain design and manufacturing practices. By leveraging the latest technology, manufacturers are making the roller chain more innovative, efficient, and responsive to the needs of modern industries. This blog explores the top key trends in the roller chain industry that are acting as a driving force for the market.
Check it out: Types of Conveyor belts
Introduction to Roller Chains
Roller chain or bush roller chain is the most common type of chain used for the transmission of mechanical power or any kind of domestic, industrial and agricultural machinery. These are typical chain link structures where a series of cylindrical rollers are connected by links. A rotating sprocket connected to the motor moves the chain and the other end of the chain is then attached to the load. Roller chains are an inevitable part of multiple industries and are known for their durability, reliability, and efficiency in power transmission.
Top key trends that are reshaping the roller chain market:
- Innovative Manufacturing Techniques
The availability of advanced materials for roller chain design and manufacturing is driving the change for the better. Traditionally, the roller chains were made from carbon steel. Though carbon steel is durable and cost-effective, it is not the right fit material for high-performance applications. As a result, Roller chain manufacturer are turning to other options like stainless and alloy steel to enhance the performance of roller chains. These advanced materials can withstand adverse operating conditions, extreme temperatures and chemical exposure without hampering their performance. While designing, the Roller conveyor safety must also be considered. While lifting applications should consider a safety factor of more than 10, a chain designed for fatigues must have the same of 7. - Focus on Quality and Durability
With the use of advanced materials, the quality and durability of the roller chains have also taken the front seat. The use of high-strength alloys and engineered plastics offers superior wear resistance and corrosion resistance, improving overall durability. The use of advanced coatings, like nickel-plating and specialized lubricants, further improves the chains’ resistance to environmental factors, reducing maintenance costs and downtime. In addition, the combination of innovative coatings and surface treatments revolutionizes roller chain durability and wear resistance. Special coatings like nickel, zinc and black oxide protect against corrosion and wear, thereby enhancing its service life. - Technological Advancements in Roller Chains
Apart from advancements in Roller Conveyor manufacturing, significant innovations in technological design are also playing a great role in enhancing chain efficiency. One such example is precision roller chains that are designed to provide greater precision and efficiency in power transmission. The integration of the Internet of Things (IoT) and smart technologies into the roller chain has paved the way for real-time monitoring and predictive maintenance capabilities of the chain. Equipped with sensors, these rollers collect and transmit data on operating conditions, temperature, vibration and wear. The team can then use this data to identify potential issues and schedule maintenance activities, thereby reducing downtime and increasing overall productivity. - Challenges and Solutions in the Industry
Corrosion, fatigue and wear limit the lifespan of roller chains. To maximize a useful life, sufficiently lubricating the chain is recommended. Also, corrosion can accelerate the effects of wear and fatigue. To save the roller from this, make sure that the chain is protected. A properly lubricated chain can minimize exposure to the environment and extend product life. - Noise reduction
Advanced features like optimized tooth profiles, vibration-damping materials, and improved lubrication systems contribute to noise reduction. A noise-free environment reduces the risk of noise-induced hearing loss in the workers and boosts workplace safety and productivity. - Engineering precision
The modern chains are engineered to provide higher precision in motion control, ensuring consistent and accurate performance. This is crucial in industries like robotics and aerospace, where precision is of the highest importance. Roller chain manufacturer achieve this through improved manufacturing processes, tighter tolerances, and advanced quality control measures. - Future Trends and Predictions
The industrial roller chain market is experiencing a steady market boom and global expansion. Emerging economies are investing heavily in infrastructure development and manufacturing. This, in turn, is fuelling the demand for reliable power transmission solutions. There has been an increase in chain demand in established markets as well. This further drives innovation and product development to meet diverse market needs.
Also read: Applications and Benefits of Chain Conveyors
Bottom Line
Drive operational efficiency and contribute to sustainable industrial growth with Delta Stark’s Roller Conveyor chains. Streamline your operations with our latest tech-led roller chains and meet the unique requirements of different industrial processes. Contact us today.