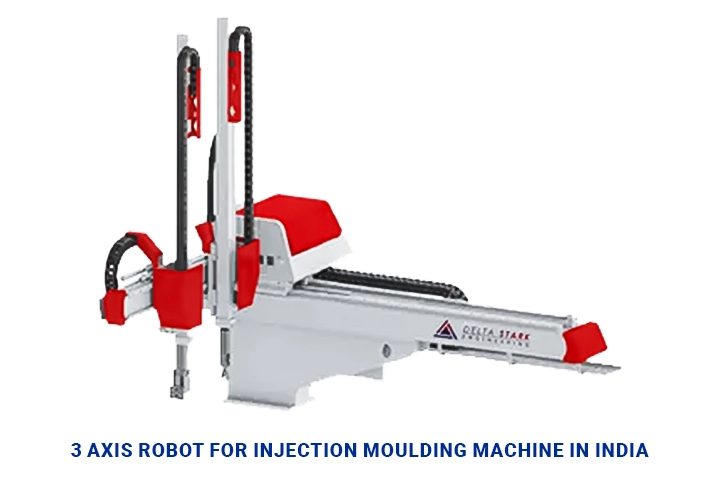
A 3 axis robot for an injection moulding machine in India is quite a vital technology in improving the efficiency and precision of manufacturing. It handles and processes the moulded parts automatically, thus significantly reducing cycle times and limiting human errors. For example, a 3-axis servo robot functions along the X, Y, and Z axes, allowing for points of picking, placing, and orienting of components. Robots are most useful in injection mouldings during operation by fastening removal of produced parts from moulds, then locating them to their respective places, and to some extent even carrying out other minor actions such as cutting or assembling. Injection moulding using 3 axis robots increases speed, consistency, and quality control.
Key Features of 3 Axis Robots
Here are the important features of 3-axis robots:
- High Speed: For speedy movement, reduce cycle times, and raise productive power.
- Versatility: To take care of various applications like pick-and-place tasks as well as assembly and material handling tasks
- Compact Design: Space-efficient in nature, suitable for integration into a small workspace environment.
- Strong Build: It is durable and made to withstand all the conditions in an industry for a long life and durability.
- Integration: Easy integration with existing systems and equipment, including injection moulding machines.
- Repeatability: High repeatability ensures performance and quality control consistency on some production lines.
Advantages of Using 3-Axis Robots in Injection Moulding
Using injection moulding with 3-axis robots it has many benefits associated with it, as follows:
- Reduced Labor Cost: Minimized manual labour reduces labour costs and redirects the human workforce to more value-added functions.
- Improved Safety: Robots may handle toxic materials and tasks that may otherwise cause human workplace injury.
- Easy Reprogramming: It can be easily reprogrammed for different products or tasks, allowing manufacturers to adapt quickly to changing production needs.
- Interfacing with Other Technologies: Easy interoperability with other automation technologies for increased efficiency in production as a whole.
- Scrap Savings: Precise results mean that very few materials are wasted, and bad output is minimal. This directly translates into lower production costs.
- Data Creation: The robots can be engineered to carry sensors that monitor the production process and offer opportunities for optimisation in real-time, always striving to improve.
Integration of 3 Axis Robots with Injection Moulding Machines
This integration of 3-axis robots with injection moulding machines is done to serve the following:
- Seamless Communication: A shared interface between the robot and the injection moulding machine allows it to work in tandem and immediately remove parts after moulding.
- Robot Handling: After the injection moulding cycle, the robot picks up the moulding from the mould. It thereby removes the scope for human error and fastens the production cycle.
- Customized Gripper Solutions: To design 3-axis robots, specific grippers are applied that can handle diversified geometries and sizes, thereby contributing to the process’s high flexibility.
- Safety Features: Integration includes safety protocols, such as emergency stop functions and safety barriers, allowing operators to operate machinery safely.
- Better Quality Checking: Vision systems installed on the robot allow for real-time scanning of parts for quality specifications before packaging.
Factors to consider while selecting the 3-Axis Robot
When selecting a 3-axis robot for use in injection moulding, among other applications, the following considerations are essential:
- Reach and Workspace: Assess the robot’s reach to ensure it features an appropriate work area reach and accessibility to moulds or production lines.
- Speed and Accuracy: Test the robot’s ability to complete the production cycle at its maximum speed while ensuring precise quality in output.
- Integration Capabilities: Ensure that the robot integrates well with the injection moulding machine you may use and other automation systems you will likely have.
- Safety: Inbuilt safety features should include, but are not limited to, emergency stops, safety barriers, and proper sensors to safeguard operators.
- Durability and Reliability: Choose a robot fabricated to handle rugged manufacturing environments over a long period, ensuring long-term reliability.
- Support and Maintenance: Determine if the manufacturer or supplier offers technical support and service options to ensure that the equipment continues to run.
Also read: The use of Industrial robots
Bottom Line
In conclusion, 3-axis servo robots are a great leap into manufacturing automation. They enhance the performance and accuracy of work and reduce the labour force, making them crucial for modern production environments. In the future, when three-axis robots are needed to provide higher quality and higher speed for the high production demand, it will become easy for manufacturers to adopt them. On the other hand, the scope for automation of repetitive tasks helps reduce human errors to the minimum level and increases workplace safety. Eventually, the strategic use of the systems will ensure businesses are better positioned in an ever-evolving market.