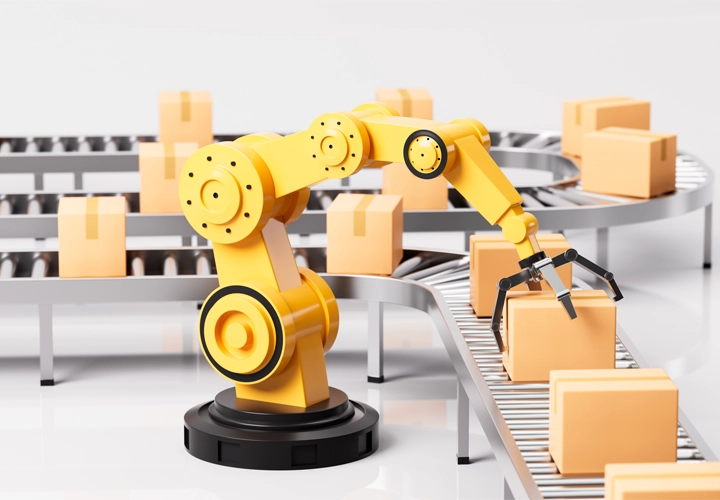
Part handling robots are an essential part of the modern injection moulding machine setup. These automated systems manage the movement of parts and materials with high precision, improving both efficiency and productivity. By streamlining material loading, part removal, and other critical processes, they help reduce cycle times and manual labour while ensuring better product quality.
What is Injection Moulding?
Before exploring the role of part handling robots, it’s important to understand what injection moulding is. Injection moulding is a manufacturing process where heated plastic material is injected into a mould cavity to form components. It is widely used to produce a range of plastic products and injection moulding machine parts, from small intricate pieces to large industrial items.
How Part Handling Robots Improve Efficiency in Injection Moulding Machines
In an injection moulding machine, part handling robots significantly enhance operations by:
-
Automating the unloading of finished parts
-
Loading raw materials into the machine
-
Reducing cycle time and manual interventions
-
Minimising product defects by precise handling
-
Increasing operator safety by replacing manual lifting and repetitive tasks
-
Providing real-time data for process optimisation
These benefits allow companies to achieve higher output, lower labour costs, and more consistent product quality.
Key Types of Part Handling Operations in Injection Moulding
Part Extraction
Description: Robots quickly and carefully extract moulded components after the cooling stage.
Benefit: Reduces cycle time and prevents damage to injection moulding machine parts.
Material Loading
Description: Automatic systems load raw plastic pellets into the injection moulding machine continuously.
Benefit: Reduces manual handling and prevents process delays.
Quality Inspection
Description: Robots equipped with vision systems inspect parts for flaws.
Benefit: Improves quality control and lowers the risk of defective products reaching the market.
In-Mould Labelling and Insert Placement
Description: Robots can insert labels or small components into the mould before injection.
Benefit: Improves product branding and functionality without manual work.
Integration Challenges and Solutions for Injection Moulding Machines
While part handling robots add substantial value, integrating them into existing injection moulding processes may present challenges:
Compatibility with Existing Systems
Solution: Assess and upgrade injection moulding machine parts and control interfaces for seamless communication between robots and machines.
Programming Complexity
Solution: Opt for robotic systems with intuitive, user-friendly programming tools and ensure adequate training for operators.
Safety
Solution: Implement proper safety measures like light curtains and emergency stops to protect workers.
Initial Cost
Solution: Conduct a thorough cost-benefit analysis to understand long-term savings. Explore financing options to reduce the upfront investment.
Maintenance and Downtime
Solution: Schedule routine maintenance for both the robot and the injection moulding machine to minimise unplanned downtime.
Data Communication
Solution: Use robust industrial networking solutions to ensure seamless data sharing between robotic systems and machines.
Customization
Solution: Choose flexible robotic solutions that can adapt to different part shapes and sizes, allowing quick changeovers.
Maximising Efficiency with Automation in Injection Moulding Machines
To fully leverage part handling robots, companies can take the following strategic actions:
-
Choose robots that match the size, reach, and payload capacity required for the specific injection moulding machine parts.
-
Deploy collaborative robots for safe interaction with human operators.
-
Integrate advanced vision systems for accurate part placement, orientation, and real-time inspection.
-
Implement continuous material feeding automation to keep the moulding process uninterrupted.
Emerging Trends in Injection Moulding Robots
Innovations continue to improve the capabilities of robots that support injection moulding machines. Some of these trends include:
-
Collaborative robots (cobots) that enhance safety and flexibility.
-
Advanced vision and AI-driven systems that improve accuracy in part handling.
-
Adaptive gripping technologies that enable robots to handle a diverse range of part shapes and materials.
-
Modular robotic designs that can be reconfigured easily to suit different tasks and injection moulding machine parts.
-
Sustainable automation solutions that reduce energy consumption and material waste.
Understanding Injection Moulding Robots
Injection moulding robots support every stage of the injection process — including part extraction, material loading, in-mould labelling, and inspection. Available in different axis configurations (3, 5, or 6 axes), they provide unparalleled flexibility. Connected to smart factory networks, they help monitor production, optimise performance, and predict maintenance needs.
Conclusion
Part handling robots help injection moulding machines achieve new levels of precision, speed, and safety. By automating critical processes and integrating smart technologies, they enhance productivity and product quality across industries. Companies looking to compete in today’s market can improve their injection moulding machine performance and reduce costs with these robotic solutions. At Delta Stark Engineering, we specialise in helping you implement the right automation solutions to optimise your injection moulding process for long-term success.