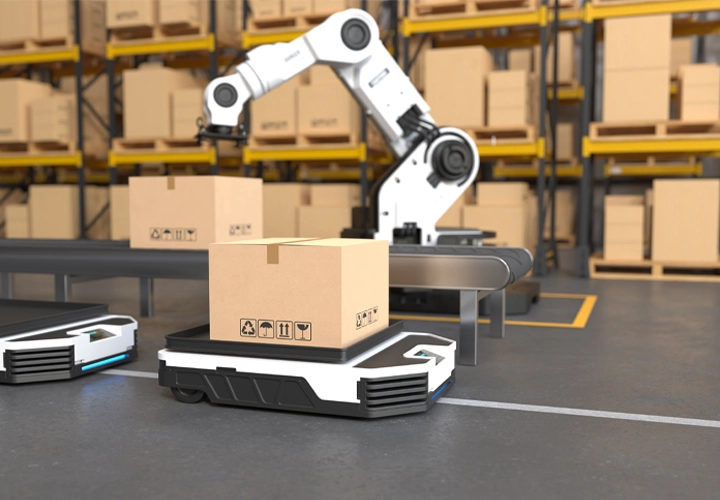
Industrial robots are transforming the injection moulding industry by automating processes, enhancing precision, and boosting overall productivity. Here’s an in-depth look at how these robotic systems are revolutionising manufacturing.
Key Contributions of industrial robots for injection moulding machines
- Automated Material Handling
Robots take over repetitive and labour-intensive tasks such as loading and unloading moulds, transferring parts, and packaging. This reduces reliance on manual labour and minimizes human error. - Precision and Consistency
Robots ensure each component is accurately positioned and handled during the moulding cycle. This consistency improves product quality and reduces scrap. - Reduced Cycle Times
By speeding up material transfers and task execution, robots significantly reduce cycle times and improve production throughput. - Enhanced Workplace Safety
Robots handle hazardous operations like managing hot or sharp components, creating a safer environment for human workers. - Flexible and Adaptable Systems
Modern robots can be reprogrammed and adapted for various moulding applications, enabling quick changeovers and customisation. - Cost Savings Over Time
Despite a high initial investment, long-term gains in productivity, reduced errors, and lower labour costs make robots cost-effective. - Scalable Automation
Robotic solutions can be easily scaled up to meet growing production demands, making them ideal for expanding operations.
Types of Industrial Robots Used in Injection Moulding
- SCARA Robots
Ideal for high-speed, horizontal pick-and-place tasks and assembly operations. - Cartesian (Gantry) Robots
These operate along three linear axes and are commonly used for repetitive, precise tasks such as loading, unloading, and stacking. - Customized End-of-Arm Tooling (EOAT)
EOAT enhances robot functionality for specific operations like gripping, cutting, or assembling moulded parts.
Advantages of Robotic Integration in Injection Moulding
- Increased Productivity: Continuous, high-speed operations without fatigue.
- Superior Quality Control: Consistent, precise movements reduce defect rates.
- Improved Safety: Minimizes direct human interaction with dangerous processes.
- Energy and Material Efficiency: Optimized processes lead to less waste and lower power consumption.
Challenges in the Indian Market
- High Capital Investment: Many small to medium enterprises (SMEs) struggle with the upfront costs of robotic systems.
- Shortage of Skilled Labor: There is a need for more trained professionals capable of managing, maintaining, and programming robots.
- Resistance to Change: Cultural preferences for manual labour and fear of job loss can slow down automation adoption.
- Infrastructure Limitations: Power supply inconsistencies and lack of digital infrastructure can hinder robot deployment.
- High Maintenance Costs: The need for specialized maintenance personnel and parts can drive up operational costs.
- Uncertain ROI: For low-volume manufacturers, the payback period may be longer.
- Customization Requirements: Robots often need to be adapted for varied mould geometries and part types.
- Technology Gaps: Older equipment may not integrate easily with modern robotics, requiring additional investment.
- Regulatory Hurdles: Navigating India’s labour laws and import duties can complicate automation efforts.
- Limited Vendor Ecosystem: A shortage of reliable domestic robotics providers and inconsistent after-sales support are additional challenges.
Conclusion: A Strategic Path Forward
Despite the challenges, industrial robots offer unmatched advantages in injection moulding. Indian manufacturers can greatly benefit from embracing automation to increase output, improve quality, and ensure safer workplaces. Companies like Deltastark provide customized robotic solutions that support seamless integration into existing moulding processes.
As the demand for smarter and faster manufacturing continues to grow, investing in robotic automation is no longer optional — it’s essential. Future-ready businesses must act now to stay competitive and sustainable in an evolving global market.