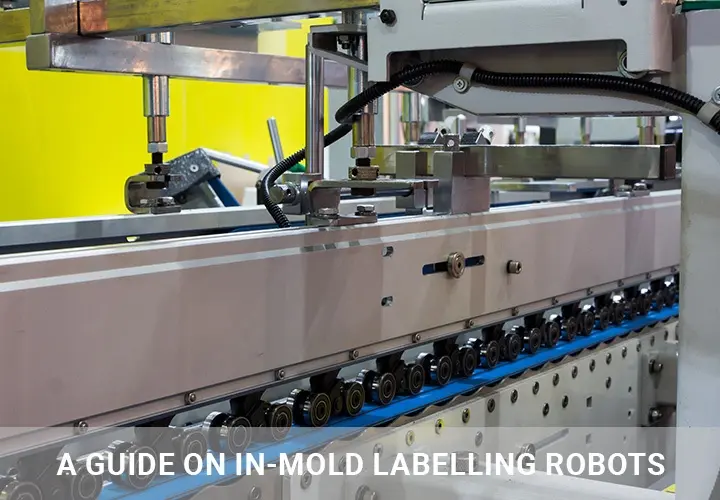
In today’s rapidly evolving plastic industry, automation has become indispensable for optimizing processes and maximizing efficiency. In-Mold Labeling (IML) robots represent a pinnacle of innovation within the injection molding process, offering unparalleled precision, speed, and versatility. In-Mold Labeling Robots (IML Robots) are cutting-edge industrial automation solutions designed to streamline the process of labeling molded products directly within the mold cavity during the injection molding process. This innovative technology offers several advantages over traditional post-molding labeling methods, including increased efficiency, improved product quality, and enhanced flexibility.
IML robots are equipped with advanced robotic arms, precision vision systems, and sophisticated control systems, allowing them to handle and place labels with utmost accuracy and consistency. The process involves inserting pre-printed labels or films into the mold cavity before injecting molten plastic, thereby seamlessly integrating labeling into the molding cycle. Unlike traditional post-molding labeling methods, IML robots insert labels directly into the mold cavity before injection, resulting in a fully automated labeling process. With the use of sophisticated technologies like robotic arms, vision systems, and programmable logic controllers (PLCs), these robots are able to precisely insert labels and coordinate with injection molding equipment.
Check out the related products: Top Entry IML Robots and Side Entry IML Robots
Key Components and Features of In Mold Labeling Robots:
- Advanced vision systems utilize cameras and sensors to detect mold features and guide the robotic arm with pinpoint accuracy during label placement.
- PLCs serve as the control center, orchestrating the movements and operations of IML robots in synchronization with injection molding machines.
- Specialized attachments such as grippers or suction cups at the end of the robotic arm facilitate the handling and placement of labels within the mold.
- IML robots feature standardized communication interfaces, allowing seamless integration with injection molding machines and other industrial automation equipment.
- IML robots are equipped with multi-axis robotic arms capable of intricate movements for precise label insertion into the mold cavity.
IML robots play a crucial role in automating the labeling process within injection molding operations, leading to significant improvements in efficiency, productivity, and product quality. By eliminating manual labeling tasks, these robots streamline production processes, reduce cycle times, and increase throughput. Furthermore, automation improves the overall quality of molded items by achieving precision and consistency, which boosts customer satisfaction and brand reputation.
Additionally, IML robots enable plastic manufacturers to adapt quickly to changing market demands, thanks to their flexibility in handling various label sizes, shapes, and materials.
Benefits of In-Mold Labeling Robots:
- Automation of the labeling process reduces cycle times and increases production throughput, maximizing operational efficiency.
- Precise label placement ensures consistency and accuracy, resulting in higher-quality molded products with minimal defects.
- IML robots can handle a wide range of label sizes, shapes, and materials, enabling manufacturers to diversify their product offerings and meet evolving customer demands.
- Through the optimization of manufacturing processes and the reduction of manual labor, IML robots eventually lead to cost savings and increased profitability.
- Automation reduces the risk of workplace accidents associated with manual labeling tasks, enhancing workplace safety and employee well-being.
Also read: Benefits of Side Entry IML Robots
Conclusion:
In-Mold Labeling Robots represent a paradigm shift in plastic industry automation, offering a synergistic blend of precision, efficiency, and flexibility within injection molding processes. By embracing automation and leveraging advanced technologies, manufacturers can streamline operations, improve product quality, and achieve sustainable growth in today’s competitive market landscape. As the plastic industry continues to evolve, IML robots will undoubtedly remain indispensable tools for driving innovation and operational excellence.