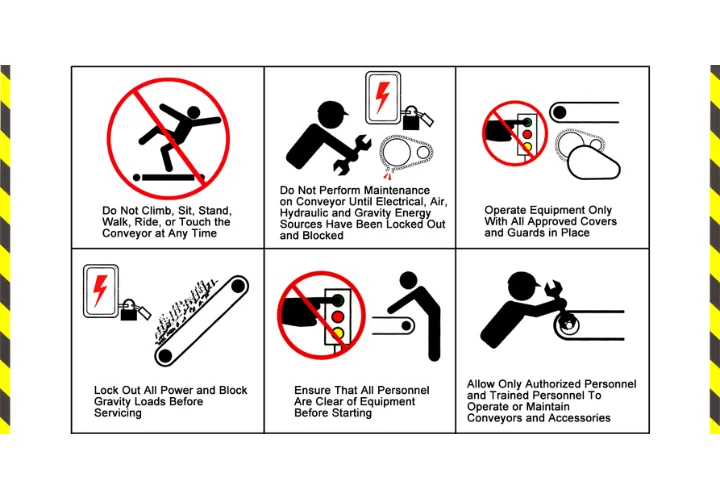
Belt Conveyors are vital in many sectors, providing efficient conveyance of materials and products. However, if not used properly, they might pose serious safety risks. As a result, adequate safety measures are critical to ensuring worker safety while simultaneously allowing for efficient product and material production. Let Delta Stark tell you about the conveyor belt safety measures in this guide.
Conveyor Controls: Common Challenges
Before we go into the best conveyor belt safety procedures, let’s review some of the most prevalent issues with these systems and why they might endanger your workplace.
Common conveyor system difficulties might include:
Belt Damage: Rips, tears, frayed edges, and other issues in Belt conveyors can be caused by abrasive or harsh materials. Other belt problems may include uneven staining or strained sections.
Blockages: Blockages can occur when things become snagged or stacked up on the production line.
Slippages and Spillages: Belt lagging, worn pulleys, or heavy loads can all cause materials to slide off the belt during production.
Mistracking: If the conveyor belt is not properly oriented, materials or other things will quickly go off track.
Seized Rollers: Ultimately, conveyor system rollers can wear and tear, potentially resulting in sharp edges. It can damage objects on the conveyor line and pose a safety risk to workers.
Carryback: Carryback happens in Roller conveyors when material accumulates in the system and causes a blockage, resulting in system dysfunction and associated safety issues.
Conveyor system problems can be frustrating, but many can be prevented if the conveyor system is examined and serviced regularly. It’s vital to note that if you don’t check and repair conveyor system faults as soon as possible, you may face extended wait periods for repairs which results in delaying output and reducing profitability.
4 Safety Practices for Conveyor Belt Systems
Conveyor belt systems – be they belt, chain, or slat conveyors – are critical in the industrial business, but they can offer a substantial safety concern if not properly managed or maintained. That’s why conveyor safety equipment and other safety measures become vital
Ensure Proper Training
All individuals who operate or work near conveyor systems must be properly trained. This training should address the system’s safe operation, emergency stops protocols, and how to promptly detect and report potential hazards. It is also critical that all employees understand the dangers connected with the Belt or Chain conveyors & know how to process them if any issue occurs.
Personal Protective Equipment Is Essential
Workers who operate near conveyor systems must wear proper Personal Protective Equipment (PPE). It may include safety glasses, gloves, hard helmets, steel-toed shoes, and other protective equipment. Employers in manufacturing should give this sort of equipment. Workers must always use personal protective equipment (PPE) to avoid injury from risks such as flying debris, pinch points, or entanglement.
Avoid Long Hair and Loose Clothes
Workers must avoid wearing long hair untied or loose clothes near conveyor systems as these can get caught in the moving parts, creating serious safety hazards. Keeping hair tied back and wearing fitted clothing reduces the risk of accidents.
Adequate Guarding and Barriers Must Be In Place
Conveyor guards and barriers for conveyor systems are critical to keeping workers away from moving parts. Adequate guarding should be installed at all entry points and around any hazardous parts of the system, even during emergency pauses. These barriers should never be removed because they protect their workers from internal moving parts and inadvertent startup.
Make Regular Maintenance A Priority
Regular maintenance and upkeep are essential to guarantee that the conveyor system operates effectively. It involves evaluating and cleaning belts, rollers, and other components to avoid wear and tear that might cause problems. Conveyor systems should be greased regularly to avoid friction & any broken components should be replaced. When doing maintenance on a conveyor system, turn off all power sources, including electric, hydraulic, and air. Always keep the area around the conveyor system clean to limit the danger of accidents and guarantee that the system runs smoothly.
Ensuring these safety measures are followed allows workers to safely work around conveyor systems, reducing potential hazards and maintaining productivity.
Latest Conveyor Safety Innovations in 2025
Industrial automation has evolved, and so have conveyor belt safety systems. Modern factories are increasingly integrating smart technologies such as:
-
AI-Powered Predictive Maintenance: IoT sensors now monitor belt tension, motor temperature, and vibration in real-time, predicting failures before they occur.
-
Automated Emergency Shutoffs: AI-integrated vision systems can detect a person or object too close to the belt and trigger instant shutdowns.
-
Laser-Based Alignment Systems: These reduce mistracking issues significantly, especially in high-speed operations.
These innovations not only reduce downtime but also drastically improve workplace safety.
Updated Indian Safety Regulations for Conveyor Systems
As of 2024-2025, India has tightened safety mandates for industrial equipment under the Factories Act and OSHA India Guidelines, including:
-
Mandatory guarding for all pinch points and nip zones.
-
Periodic inspection logs for all powered conveyors.
-
Requirement to implement lockout/tagout (LOTO) systems for maintenance.
-
Noise-level compliance in enclosed conveyor rooms.
If you’re operating in India, aligning with these updated norms is essential to avoid penalties and ensure compliance.
Eco-Friendly Belt Conveyors: Sustainability Meets Safety
With sustainability becoming a major focus, many manufacturers are now adopting eco-safe conveyor designs, which also enhance safety:
-
Low-noise, energy-efficient motors to reduce fatigue and environmental stress.
-
BPA- and lead-free belts that reduce toxic exposure.
-
Recyclable components and modular designs that make maintenance cleaner and safer.
Delta Stark integrates these eco-safety designs into every system to support your green goals.
Safety Training: VR and Simulation for Conveyor Operators
Traditional safety training is now being replaced by VR-based training modules:
-
Operators and maintenance crews can experience real-time hazard scenarios in a virtual setup.
-
Helps workers understand what to do during a blockage, spill, or roller seizure, without putting themselves at risk.
-
Improves retention of safety protocols and reduces onboarding time.
Delta Stark offers training resources or partners with safety training providers to upskill your workforce with modern methods.
Smart Maintenance Scheduling with Conveyor Monitoring Apps
Thanks to mobile integration, you can now:
-
Receive real-time alerts on belt alignment, load inconsistencies, or overheating via an app.
-
Track inspection and lubrication schedules.
-
Log photos and notes directly for audit and compliance.
Delta Stark recommends implementing these apps for multi-facility operations or high-load environments.
Wrapping Up
All of these safety measures, if strictly followed, will assist in preventing any safety issues associated with conveyor belts in your operation. However, people working with and near conveyor systems must stay vigilant for possible risks.
To keep your staff and facility safe, you must maintain constant awareness, receive adequate training, and use well-designed conveyor systems with proper safety measures. In terms of workers, it is better to be safe than sorry. By leveraging safe belt and Safetrak conveyor resources, you can ensure maximum safety and efficiency in your operations. And we are the belt conveyor manufacturer you can trust!
Contact Delta Stark today to learn more or arrange maintenance on your conveyor belt system.