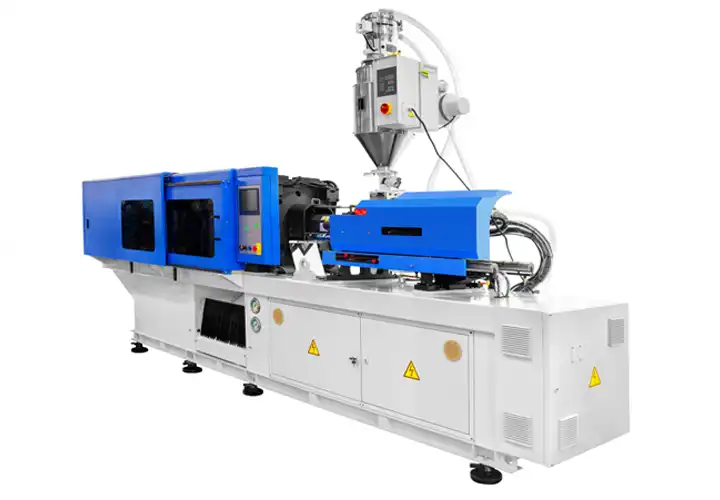
Introduction
Injection moulding is a widely used manufacturing process that shapes plastic materials into precise components for various industries. From automotive and medical to consumer goods and electronics, this method enables mass production of complex plastic parts with high efficiency and accuracy. The performance of this process relies heavily on the type of injection moulding machine used. But how many types of injection moulding machines are there, and which is right for your production needs? In this blog, we’ll break down the key categories, their features, applications, and how to choose the best one.
What is an Injection Moulding Machine?
An injection moulding machine is a device that heats plastic resins until molten and injects them into a mould cavity. Once cooled and solidified, the material takes the desired shape. The machine’s configuration and technology determine how efficiently it performs this task, depending on the product and material type.
Types of Injection Moulding Machines by Drive System
1. Hydraulic Injection Moulding Machines
- How it works: Uses hydraulic pumps to generate clamping and injection force.
- Best for: Large, heavy parts and bulk production.
- Pros: High clamping force, low initial cost.
- Cons: Higher energy use, more maintenance.
2. Electric Injection Moulding Machines
- How it works: Operated by servo motors for movement and pressure.
- Best for: Cleanroom applications, precision parts.
- Pros: Energy-efficient, quieter, faster cycles.
- Cons: Higher upfront cost.
3. Hybrid Injection Moulding Machines
- How it works: Combines hydraulic and electric systems.
- Best for: Versatile manufacturing needs.
- Pros: Balanced energy efficiency and power.
- Cons: Slightly more complex to maintain.
Types by Machine Orientation
1. Horizontal Injection Moulding Machines
- Common in: Most industries.
- Benefits: Easy automation, ideal for high-volume production.
- Applications: Automotive parts, containers, appliance housings.
2. Vertical Injection Moulding Machines
- Common in: Insert moulding, space-limited setups.
- Benefits: Gravity-assisted loading, compact layout.
- Applications: Electrical components, embedded metal inserts.
Types by Material Processed
1. Thermoplastic Injection Moulding Machines
- Process: Melts and reshapes thermoplastics repeatedly.
- Materials: Polypropylene, ABS, PVC.
- Industries: Packaging, toys, consumer goods.
2. Thermoset Injection Moulding Machines
- Process: Cures materials into a permanent shape.
- Materials: Epoxy, phenolic, melamine.
- Industries: Electrical, heat-resistant parts.
3. Metal Injection Moulding (MIM) Machines
- Process: Combines metal powders with binders.
- Applications: Precision metal parts like gears, brackets, dental tools.
Specialised Injection Moulding Machines
1. Multi-Material Injection Moulding Machines
- Function: Injects two or more materials in one cycle.
- Use Case: Multi-colour, multi-property components.
2. Micro Injection Moulding Machines
- Function: Produces very small, intricate parts.
- Use Case: Medical devices, microelectronics.
3. Liquid Silicone Rubber (LSR) Injection Moulding Machines
- Function: Processes heat-cured silicone.
- Use Case: Flexible, durable components like baby bottle nipples, gaskets.
How to Choose the Right Injection Moulding Machine
Before selecting a machine, consider the following:
- Material Requirements: Thermoplastic vs thermoset vs metal.
- Part Size & Complexity: Larger parts may require hydraulic; micro parts need high precision.
- Production Volume: Electric for fast, high-volume; hybrid for flexibility.
- Budget & Energy Use: Weigh initial costs against long-term energy savings.
- Automation Potential: Consider integration with robotics for enhanced efficiency.
Conclusion
So, how many types of injection moulding machines are there? At least 11 widely recognised types, each with unique features suited for specific tasks, materials, and industries. From heavy-duty hydraulic machines to precision electric units and flexible hybrids, the choice of machine directly impacts your production quality and cost-efficiency.
At Delta Stark Engineering, we help you identify and implement the perfect injection moulding solutions based on your application needs. Whether you’re in automotive, electronics, or consumer products, our automation systems, including pick-and-place robotics, enhance your manufacturing success.
Ready to upgrade your production line? Contact Delta Stark Engineering for expert consultation and tailor-made solutions.