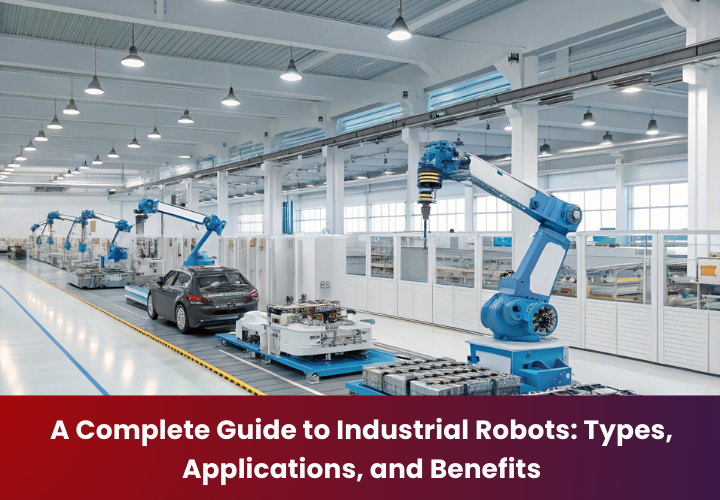
It’s considered a necessity to have industrial robots in a fast-moving manufacturing world. These intelligent machines are changing global industries by keeping production flowing and applying precision to very complex tasks. Industrial robot manufacturers will work toward designing smarter, faster, and reliable systems, responding to the needs of these demanding times. This is a guide that will detail the different types of industrial robots, their applications, their benefits, and how different companies can maximise the utilisation of these robots.
What is an Industrial Robot?
An industrial robot is a mechanical device designed to automate and execute complex industrial tasks. These robots are reprogrammable, multifunctional, and designed to move materials, parts, tools, or specialized devices through various programmed motions. They are widely used to increase productivity, precision, and safety in industrial environments. Examples include robotic arms for welding, SCARA robots for assembly, and delta robots for high-speed picking.
What Are Industrial Robots? – A Modern Revolution in Automation
Industrial robots are programmable, automated machines designed to perform a wide variety of manufacturing tasks with precision, speed, and minimal human intervention. These mechanical systems are capable of welding, assembling, painting, packaging, and more—making them indispensable across automotive, electronics, food, pharmaceuticals, and metal industries.
Unlike traditional machinery, industrial robots are equipped with sensors, actuators, and AI-driven control systems that allow them to adapt to real-time feedback, ensure consistency, and work tirelessly 24/7. Their ability to operate in hazardous environments, handle heavy loads, and maintain high-quality standards makes them a cornerstone of smart factories and Industry 4.0 transformation.
Key Highlights of Industrial Robots:
-
Flexibility: Easily reprogrammable for multiple tasks and products.
-
Precision: High repeatability ensures product quality and accuracy.
-
Scalability: Ideal for both small batch and mass production environments.
-
Efficiency: Drastically reduces cycle times and improves overall throughput.
-
Safety: Minimises human exposure to risky or repetitive work.
Whether it’s a robotic arm used for welding car parts or a delta robot picking and placing food items at lightning speed, industrial robots are shaping the future of global manufacturing.
Types of Industrial Robots
Industrial robots come in different forms, for different tasks, and in different environments:
Articulated robots– Rotary joints imitate human arm-like movement, welding, material handling, and packaging.
SCARA Robots– More rigid than articulated robots, these robots excel in pick-and-place tasks and also in high-speed assembly.
Cartesian robots- Carry out operations on three linear axes, which are fashionable for CNC machines, 3D printing, and heavy tasks.
Delta robots- Very fast and very precise robots, mostly used in the food and pharmaceutical industries.
Cobots: Also known as cooperative robots, they are designed to interact with humans safely, generally becoming popular in small and medium enterprises.
Key Applications of Industrial Robots
Industrial robots are extremely versatile and find application in some areas:
Welding and Soldering: Very popular in the automotive and aerospace industries, providing consistent quality and speed.
Material Handling: Be it lifting or placing heavy items on a conveyor belt, robots do so effectively without human intervention.
Assembly: Precision assembly is critical in electronics and machine manufacturing.
Painting and Coating: Robots make sure of an even coat, minimise wastage, and reduce exposure to hazardous chemicals.
Quality Inspection: With the help of integrated sensors and cameras, robots are able to detect faults much faster than the human eye.
Advantages of Using Industrial Robots
The benefits of industrial robots start with:
Productivity: 24/7, no fatigue- more output is generated.
Consistency & Accuracy: Human error can be eliminated in the name of consistent product quality.
Cost-Effectiveness: It may be a significant investment, but eventually, it will save money by reducing errors, labour costs, and downtime.
Safety: Risky work can be automated, thereby curtailing workplace injuries.
Scalability: Robotic automation can easily be increased with the demand for higher production.
Industries Benefiting from Industrial Robots
Automation helps various sectors, from small businesses to multinational giants:
Automotive: The car industry was one of the first adopters, and it heavily relies on robotics for assembly and welding of the structures.
Electronics: Robots can manipulate delicate components, like resistors, capacitors, etc., with fantastic precision.
Medicine and Pharmaceuticals: Robots lend a helping hand in super-accurate packing, inspection, and laboratory automation.
Food and Beverage: Maximum speed sorting, packaging, and quality checks contribute to efficiency and hygiene.
Metal and Machinery: Cutting, drilling, and forging are faster and safer with the help of robots.
Challenges in Implementing Industrial Robotics
Although the advantages are clear, hurdles remain in the way:
- High Initial Investment: Getting and setting up robots can incur heavy costs.
- Skill Workforce: Operation and maintenance of the robots will require trained professionals.
- Integration Problems: Integrating robots into existing systems and workflows may be complex.
- Cybersecurity Issue: Protecting the systems from cyber threats would become important as robots are getting intelligent and are becoming more connected.
How to Maintain and Optimise Industrial Robots
Top robot manufacturers emphasise the fact that essential maintenance helps to yield a steady return on your investments:
- Regular Inspection: A routine checkup must be scheduled for any signs of wear and tear.
- Software Update: Ensure the systems remain updated with the latest features and security patches for the best performance.
- Monitoring of data: Analytic tools are used to monitor efficiency and pinpoint possible problems.
- Maintenance Training: Train employees to troubleshoot basic tasks and maintenance.
How to Choose the Right Industrial Robot for Your Business
Choosing the right robot is critical to maximizing ROI and operational efficiency. Consider the following when selecting a robot for industrial use:
1. Define the Application Clearly
Different tasks require different robots. For example, articulated robots are ideal for welding, while delta robots are better for high-speed packaging in the food industry. Matching robot capabilities to specific tasks avoids overspending or underperformance.
2. Evaluate Payload and Reach
Payload is the weight a robot can handle. Reach determines how far the robot can extend. Both are essential for applications like material handling robots and packaging robots.
3. Consider the Workspace Environment
Dusty, high-temperature, or cleanroom environments affect your choice. For example, robots used in injection moulding machines are often enclosed and need heat-resistance.
4. Check Integration Compatibility
The robot must work with existing machines, software, and workflows. Choose robot systems that can integrate with your MES, ERP, or PLCs.
5. Assess Scalability and Future Needs
Think long-term. Will your business scale up in the future? Go for robot solutions that can adapt—like modular robotic arms or collaborative robots (cobots) that are easy to redeploy.
Top Industrial Robot Manufacturers in India
If you’re in India or Southeast Asia, some of the top industrial robot manufacturers and solution providers include:
-
Delta Stark – End-to-end solutions for injection moulding automation, environmental testing, and material handling robots.
-
ABB Robotics – Known for high-performance articulated and SCARA robots.
-
Fanuc India – Offers reliable and scalable robots for automotive and electronics.
-
KUKA Robotics – Advanced systems for collaborative and industrial automation.
-
Yaskawa – Strong in welding, painting, and cleanroom robotics.
Application of Industrial Robots in Manufacturing
Manufacturing robots play a transformative role in modern industry. They are integrated into every stage of production—from raw material handling to final product packaging. Here’s how they revolutionize manufacturing:
- Smart Assembly Lines: Robots speed up repetitive assembly tasks, ensuring faster cycle times.
- Precision Machining: In CNC and metal fabrication shops, robots guarantee precise, repeatable cuts and welds.
- Material Movement: Automated guided vehicles and robotic arms streamline material flow across departments.
- Real-Time Quality Monitoring: Robots with vision systems inspect products during production, reducing waste and rework.
- Custom Manufacturing: With advanced programming, robots handle small-batch, high-mix production without delays.
The integration of industrial robots in manufacturing boosts productivity, minimizes human error, and ensures a consistently high level of quality—all of which are crucial in today’s competitive landscape.
Conclusion
The future of manufacturing will be the spreading of intelligent automation, a field where industrial robot manufacturers take the lead. These machines are changing industries worldwide with many types, endless applications, and indisputable benefits. By cooperating with the best manufacturers and investing in these appropriate systems, companies have a chance to optimise their operations and de-risk their investments in the industry’s future. Whether you are just scratching the surface or ready for scaling, this is the time to see what industrial robots offer.