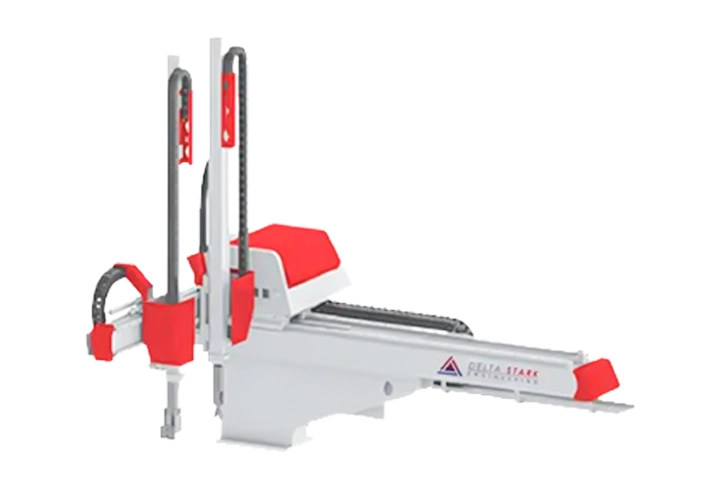
Plastic injection moulding is a widely used manufacturing process for producing plastic parts in high volumes. This process involves injecting molten plastic into a plastic injection moulding machine, where it cools and solidifies into the desired shape. The efficiency and precision of this process can be significantly enhanced by the integration of robots, known as robotic arms or automation systems, into the injection moulding workflow.
Types of Robots Used in Plastic Injection Moulding
In plastic injection moulding, single-axis, three-axis, and five-axis robots are commonly used for automating tasks like part removal, insert loading, and post-processing. These robots differ in complexity, flexibility, and the number of axes they can move along, which directly influences the tasks they can handle.
- Single-Axis Robots
• Structure: Operate along one linear axis (usually the vertical or horizontal axis).
• Function: Typically used for very simple tasks, such as picking and placing parts in a single direction.
• Applications:
– Sprue removal: A single axis robot can quickly remove sprue or runner waste from the Mold.
– Simple part ejection: The robot moves in one direction to remove parts from the Mold and place them on a conveyor or in a collection bin.
• Advantages:
– Cost-effective and simple to program.
– Suitable for basic operations in low-complexity moulding applications. - Three-Axis Robots (Cartesian Robots)
• Structure: Operate along three linear axes: X (left to right), Y (front to back), and Z (up and down).
• Function: These robots are widely used for part removal, handling, and placing tasks. They are known for their precision and reliability in handling repetitive tasks.
• Applications:
– Part removal: Picking parts from the Mold and placing them on a conveyor or in a storage system.
– Stacking and sorting: Three-axis robots can position parts in specific orientations or stacks after removal.
• Advantages:
– Reliable for simple to moderately complex operations.
– Easy to program and maintain.
– Ideal for high-speed, repetitive tasks in injection moulding. - Five-Axis Robots
• Structure: Operate along three linear axes (X, Y, Z) plus two additional rotational axes, allowing for more complex motion and orientation control.
• Function: Five-axis robots offer greater flexibility than three-axis robots and are capable of handling more complex tasks, such as orienting parts in different angles or positions.
• Applications:
– Complex part removal: Removing parts from Molds where specific orientation or rotation is required during handling.
– Insert loading: Positioning inserts into Molds that require precise angular placement.
– Secondary operations: These robots can assist with trimming, assembly, or placing parts in more intricate orientations for post-processing.
• Advantages:
– Greater flexibility and precision compared to three-axis robots.
– Capable of handling complex geometries and tasks that require rotation or more dynamic movements.
Check out our product: Multi Axis Servo Robots
Applications of Robots in Plastic Injection Moulding
Robots are increasingly used in various applications within plastic injection moulding to improve efficiency and quality. Here are some key applications:
- Loading and Feeding: Robots automate the loading of raw plastic materials into injection moulding machines, ensuring consistent material flow and reducing manual handling.
- Part Extraction: After the injection process, robots efficiently extract finished parts from the mould, minimizing cycle time and reducing the risk of part damage.
- In-Mould Labelling: Robots can place labels or inserts directly into the mould before the injection process, allowing for enhanced branding and functionality without manual intervention.
- Quality Control: Robots equipped with vision systems perform real-time inspections of moulded parts, checking for defects and ensuring that products meet quality standards.
- Assembly Tasks: Robots can perform secondary assembly operations, such as inserting components or fastening parts, reducing the need for manual labour and increasing production speed.
Safety Considerations When Using Robots in Injection Moulding
When integrating robots into injection moulding processes, several safety considerations must be addressed to ensure the well-being of operators and the efficient operation of machinery. Here are some key safety considerations:
- Risk Assessment: Conduct a thorough risk assessment to identify potential hazards associated with robot operations, including pinch points, moving parts, and interactions with human workers.
- Safety Guards and Barriers: Install physical barriers or safety guards around robotic work cells to prevent unauthorized access and protect operators from potential hazards.
- Emergency Stops: Ensure that robots and machinery are equipped with easily accessible emergency stop buttons to allow for quick shutdown in case of an emergency.
- Training and Education: Provide comprehensive training for all personnel involved with the robotic systems, focusing on safe operation, maintenance, and emergency procedures.
- Proper Programming and Controls: Implement secure programming protocols to prevent unauthorized changes and ensure that robots are correctly programmed for safe operation.
- Regular Maintenance: Schedule routine inspections and maintenance of robotic systems to ensure they operate smoothly and safely, minimizing the risk of mechanical failure.
- Collaborative Robot (Cabot) Safety: If using collaborative robots, ensure that they are equipped with safety features, such as force limiting and sensors to detect human presence, to allow for safe interaction with operators.
- Clear Communication: Establish clear communication protocols between human operators and robotic systems, using visual signals or alarms to indicate robot status and operations.
- Personal Protective Equipment (PPE): Ensure that operators wear appropriate PPE, such as gloves, safety glasses, and hard hats, when working near robotic systems.
- Monitoring and Supervision: Implement monitoring systems to track robotic operations and ensure that human operators are supervised when working near automated processes.
Choosing the Right Robot for Your Injection Moulding Operation
Factors to Consider (Payload, Speed, Precision)
When choosing the right robot for your injection moulding operation, it’s essential to consider factors like payload capacity, speed, and precision. These factors directly affect the performance of the robot and the overall efficiency of your production process. Below are key considerations for selecting the right robot:
- Payload Capacity
• What it is: The maximum weight the robot can handle, including the weight of the end-of-arm tooling (EOAT) and the parts being manipulated.
• Why it matters: If the robot’s payload capacity is too low for the parts being produced, it may experience excessive wear, decreased accuracy, or failure. Choosing a robot with an adequate payload capacity ensures it can handle the weight of the moulded parts and the EOAT efficiently.
• Key Considerations:
– Part weight: Heavier parts require a robot with a higher payload capacity.
– End-of-arm tooling weight: The EOAT itself adds to the payload. Make sure to include this weight when calculating the total required capacity.
– Material type: Some plastic materials are heavier, requiring more robust robots.
• Typical choices:
– For small, moulded parts, robots with lower payload capacities (1-5 kg) are sufficient.
– For large parts or complex multi-cavity Molds, robots with higher capacities (10-50 kg or more) are needed. - Speed
• What it is: The rate at which the robot can perform its movements, typically measured in cycle times.
• Why it matters: The speed of the robot affects the overall cycle time of the injection moulding process. Faster robots can reduce idle time between cycles, increasing production throughput.
• Key Considerations:
– Cycle time optimization: In high-speed production environments, a fast robot minimizes the time spent on part removal and other tasks, contributing to shorter cycle times.
– Task complexity: For simpler pick-and-place operations, higher speed robots like Cartesian or SCARA robots can be very effective. However, for more complex tasks, precision may be more important than speed.
– Balance between speed and accuracy: Higher speed may sometimes reduce precision, so finding the right balance is crucial based on the requirements of the part.
• Typical choices:
– For high-speed production, use robots like delta or Cartesian robots, which are optimized for fast pick-and-place tasks.
– For complex part handling, such as in insert moulding, six-axis or five-axis robots might be preferable despite being slower due to their ability to perform more intricate movements. - Precision
• What it is: The robot’s ability to place or manipulate parts with high accuracy, usually measured in millimetres.
• Why it matters: Precision is crucial when handling parts with tight tolerances, placing inserts, or conducting secondary operations like trimming or assembly. Lack of precision can lead to part damage, misalignment, or quality issues.
• Key Considerations:
– Part complexity: Complex, intricate parts or those with delicate features require higher precision to avoid damaging parts during handling.
– Insert moulding: For operations involving the placement of inserts into Molds, high precision is essential to ensure that inserts are properly placed and do not shift during moulding.
– Tolerance requirements: If the finished parts require tight tolerances, the robot must have high accuracy to ensure consistent handling.
• Typical choices:
– For simple, high-speed tasks, a three-axis Cartesian robot is often sufficient as it provides good precision in repetitive tasks.
– For complex or multi-directional tasks, a five-axis or six-axis robot offers superior precision and flexibility, especially for delicate part removal or handling operations. - Work Envelope
• What it is: The range of space or area within which the robot can operate.
• Why it matters: The robot needs to have a sufficient work envelope to reach all necessary areas of the Mold, conveyors, or post-processing stations.
• Key Considerations:
– Machine size: Larger injection moulding machines may require robots with a bigger work envelope to cover the entire Mold area and surrounding space.
– Part transfer distance: Consider whether the robot needs to place parts far away from the Mold or onto multiple conveyors.
• Typical choices:
– Cartesian robots generally have a larger work envelope suitable for part removal from large Molds.
– Articulated robots (five-axis or six-axis) can cover smaller but more complex work areas due to their flexibility. - Ease of Programming and Integration
• What it is: The difficulty or simplicity of programming the robot for specific tasks, as well as integrating it with the existing injection moulding machine and systems.
• Why it matters: A robot that is difficult to program or integrate can lead to longer setup times and potential issues in production. Ease of programming is particularly important for manufacturers with frequent part changes or varying product designs.
• Key Considerations:
– User interface: Look for robots with intuitive programming interfaces or teach-pendant systems, which simplify setup.
– Compatibility with existing systems: Ensure the robot can be easily integrated with your moulding machine’s controller and software.
• Typical choices:
– Cartesian robots tend to be simpler to program, especially for straightforward pick-and-place operations.
– Collaborative robots (cobots) are designed for easy setup and programming, often through manual guidance, making them ideal for operations with frequent changes. - Durability and Maintenance
• What it is: The robot’s ability to withstand wear and tear over time and the ease of maintenance.
• Why it matters: Reliable robots reduce downtime and maintenance costs. Durability is particularly important in high-volume production environments.
• Key Considerations:
– Cycle demands: For operations running 24/7 or with high cycle demands, choose robots known for durability and low maintenance.
– Serviceability: Consider the availability of parts and ease of maintenance for the robot.
• Typical choices:
– Cartesian robots are known for their robustness and long service life with minimal maintenance.
– Collaborative and six-axis robots often require more complex maintenance due to their additional axes and joints.
Bottom Line
In conclusion, integrating robots into plastic injection moulding processes is crucial for improving efficiency, precision, and safety. Selecting the right robot based on factors like payload, speed, and precision enhances production quality and reduces cycle times. With a focus on safety and maintenance, manufacturers can leverage robotic technology to maintain competitiveness. Deltastark is poised to provide tailored robotic solutions that meet the evolving needs of the industry.